トヨタ生産方式で最も基本となる考え方です。
そもそものきっかけは工場の現場で正常なのか異常なのかが判別できないことから始まってます。正常な状態を明確に定義すれば、それから外れた状態は異常と判断できます。
同様に、基準があれば変化がわかります。
要は、基準を定義してその差分を視覚化して管理するという考え方です。
日々の不良率を管理する例です。折れ線グラフに毎日不良率を記入します。
全体のトレンドを見ると不良の増加、現象がわかります。
目標不良率を点線で横一直線に記入すれば、日々が目標以下なのか、目標を上回り、何らかの手をうたなければいけないのかがわかります。
先週の(あるいは先月の)平均不良率が横線で記入してあれば、変化がわかります。
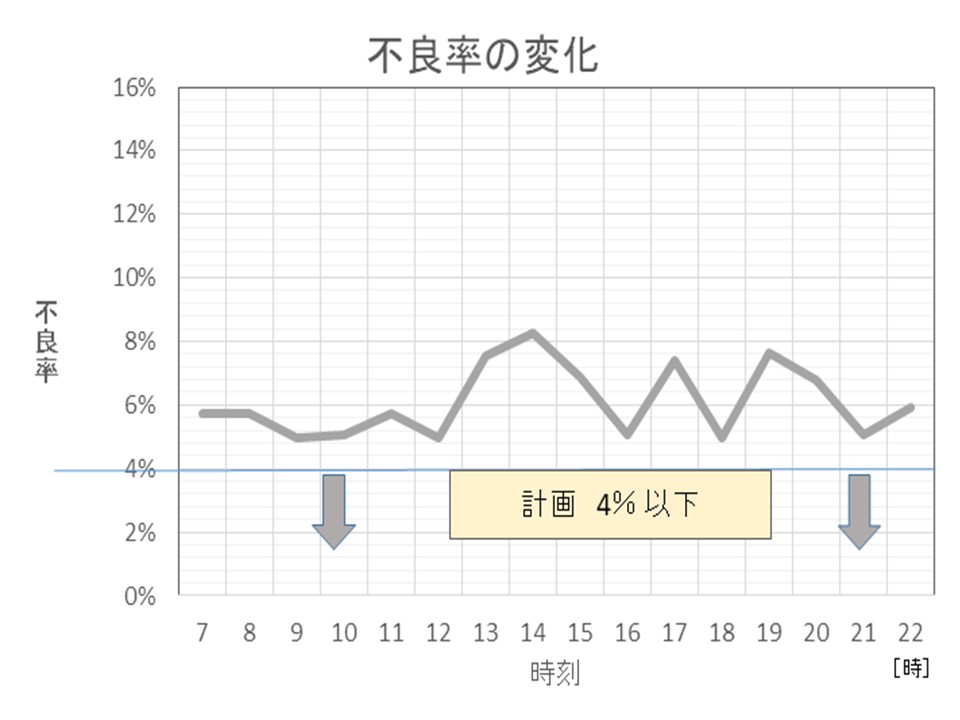
不動産会社や自動車販売店を舞台にしたテレビドラマを思い描いてください。成約件数や台数のグラフを貼り出してあります。相対比較することで優劣が視覚的にわかります。今月の目標ラインが記入してあれば、後どれだけ頑張ればよいか、誰が頑張らないといけないかがわかります。
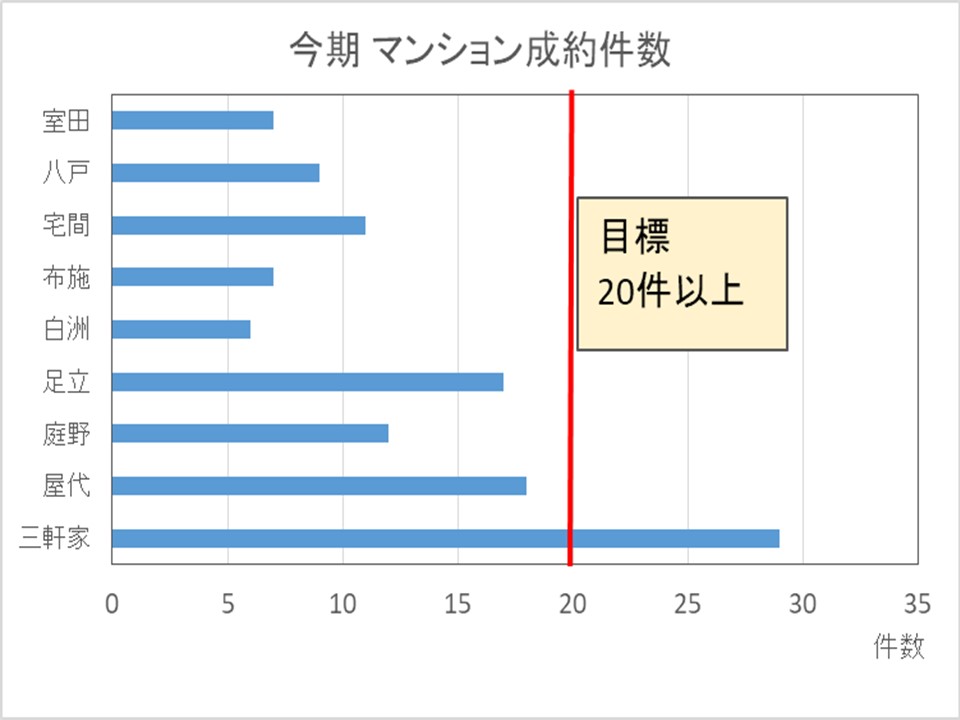
開発や研究など、日程軸の目で見る管理は、推進すべき項目ごとの予定チャートを基準として実績を並べて記入します。予定に対しての遅れ状況が視覚的にわかります。
管理状況を誰でも見えるようにするのが目で見る管理です。自信と信頼に基づいての相互の自己管理です。自信がなければ見せません。遅れや問題が見て取れて困っているときに支援してくれる体制がなければ見せません。
目的は見せることでも、管理でもありません。何のための目で見る管理なのかを明確に意識することが必須です。
目的の明確化
最も重要となる要素です。そして当たり前のことです。
よく言われるように、当たり前すぎで、かえって見逃されることです。
そして、仕事以外でも、たとえば、大学の学生の研究や、町内会の活動などなど、多くの場面で必要なことです。
- 何のための業務かを明確にします。
- 目的を宣言します。
- 同時に見える化します。
- 適宜見直します。
<補足>
・必要であれば、「何をいつまでにどうするか」で書き下します。慣れないと骨の折れるところです。メンター、指導者の方と何度も議論することで『本当の』目的として言葉にできます。私の場合は、数々の上司がメンターでした。もちろんOJTです。
・宣言とは、関係者や周りのみんなが見えるようにするケース、自分の中で自分に宣言するケース、いろいろ状況も考えて決めましょう。
・見える化とは、常に確認できる状態とすることです。職場に掲示するような文化があれば、掲示して誰でも見れるようにするといいでしょう。そのような文化がなかったり自分個人レベルであれば、PCのデスクトップやリアルなデスクに表示するなど事有るごとに視界に入るようにしましょう。常に進行内容が本当の目的に沿っているかどうかの確認です。ズレていたらもちろん進行内容を修正します。
・環境の変化で出口の目的を変更すべき状況となっていないかを適宜確認します。場合によってはその業務の必要性が失われているかもしれません。
トヨタのA3文化、紙一枚にまとめる文化においても、まずは、この目的の明確化から始まります。
基準の明確化/再確認
トヨタ生産方式導入の一歩目は、基準を明確にすることです。
基準は他人との会話のために必須です。
そして自己管理のためにも重要です。
秀吉が、枡のサイズを京枡に統一したことは基準の明確化の例ですね。
・基準設定の目的を明確にします。
・可能な限り、シンプルな基準とします。
・基準が無い場合は、定義を明確として、新たに基準を設定します。
・基準を変更する際は、新旧の差を定量的に定義して、「行き来」できるようにします。
<補足>
・不良を低減するための不良率、生産性管理のための出来高、研究進度確認のための指標など、何のための基準化かを明確にします。誰から見ても同じ基準とならなければいけません。
・誰でも、必要な瞬間にすぐに使える基準でないと運用は継続できません。
TPSでは4S(あるいはしつけを含めて5S)を徹底しますが、これは、モノの存在に対する定義の明確化です。
・時系列的な変化やその場にいない人との会話のために基準は必要です。そのためにはまずは基準を作る必要があります。どうにも間尺に合わないが、いい知恵が出ないときは仮の基準として定義しましょう。
・より合理的な基準が見つかった際や、環境変化で基準の運用に手間暇が生じるようになった際、基準を変更する必要がありますが、継続的に管理や会話ができるために、新旧の換算方法を定量的に決めておく必要があります。この換算の考え方があれば、基準に対する捉え方は柔軟となります。もちろん、あまりにしばしばの基準変更はいけません。
見える化と見せる化
しばしば、トヨタの「見える化」、サムスンの「見せる化」と説明しております。
「見える化」とは、トヨタ生産方式(TPS)でしばしば登場する言葉です。ただ、トヨタで仕事をしている限りでは、TPSに限らず、見える化することが常でした。予算消費状況、カイゼン提案件数、有給休暇取得日数、不良率の推移、開発日程と進度、何でもかんでも表やグラフにして、職場にペタペタと貼ったものでした。誰でもいつでも見ることができるようにすることが良いとの企業文化です。
先日、スポーツ用品メーカさんの工場を見学する機会がありました。製造現場、我々見学者も見えるところに、不良率推移グラフが貼ってありました。後日、TPSを導入されているとお伺いして納得したところです。
「見える化」するということは、見られてもいいという、自信が無いと実現しません。都合の悪い情報を出さないということも難しくなり、「見える化」している職場周辺の信頼感も高まります。「見える化」は自然発生的なレベル向上活動となり、継続的カイゼンにつながることが多いように感じます。
ちなみに、トヨタでは「見せる化」はよろしくないという評価となります。自発的自律的な自己管理としての「見える化」という文化に寄ります。
サムスンで「見える化」「見せる化」を議論したことはありません。積極的に話題になるテーマではないとの印象を持ってます。サムスン電子の常務の方は、「見える化」では価値がなく、「見せる化」することで情報に価値を生じるというようなご発言をされてます。この発言の趣旨は、トヨタ流の「見える化」に対峙する意味での「見せる化」を説明しているのではなく、戦略的に情報を活用するためには、それを見せることこそ価値があるというものです。動的な攻めの経営においてのご説明のようでした。経験上、企業文化的に、サムスンでは明らかに「見せる化」は好まれます。
トヨタでの「見える化」は自発的向上活動、サムスンの「見せる化」は攻めるツールとしての主張であり、それぞれ、切り取り方が違います。どちらが良いという議論は無意味です。
不良の見える化
不良の存在を白日の下にさらす、その存在を歴然と示すということです。極めて勇気がいることです。上層部や関連部署との信頼感が無いと実現できません。
不良そのものを見えるように保管する、あるいは、不良のデータや情報、たとえば不良率の変化グラフを掲示するなどです。
不良を見える化することによって、
- 不良の定義の明確化
- 事実の共有での信頼感醸成
- 戦うべき「敵」を明確とし、一体感を持った職場としての早期解決
- 不良対策に取り組んでいるという姿勢明示
- 経験者からの意見を受ける
などのメリットを享受できます。