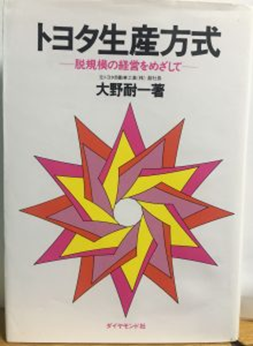
カイゼンの糸口として7つのムダの視点で観察します。
7つの着眼点をさかのぼるとトヨタ生産方式の骨子に行き着きます。
トヨタ生産方式の導入や、さらには継続のむずかしさに関してはしばしば解説してきているところです。
7つのムダの実践においても、本来的にはトヨタ生産方式の理解が必要です。
そのような背景を念頭に置きながら、7つのムダを見ていきます。
今回は 「手待ちのムダ」です。
大野耐一さん著の「トヨタ生産方式」の巻末には、付録の主要用語辞典がありますが、その中にも『ムダを意識し撲滅する』としてこの7つのムダを解説しています。
「トヨタ生産方式」by大野耐一 のご紹介
ぜひとも一度お読みいただきたい本です。
お買い求めのご参考までに、Amazonをご紹介します。
トヨタ生産方式――脱規模の経営をめざして | 大野 耐一 |本 | 通販 | Amazon
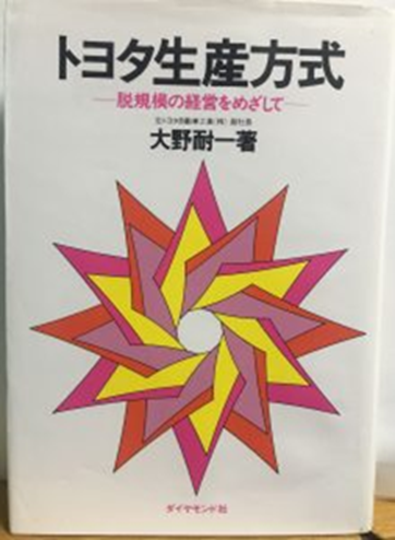
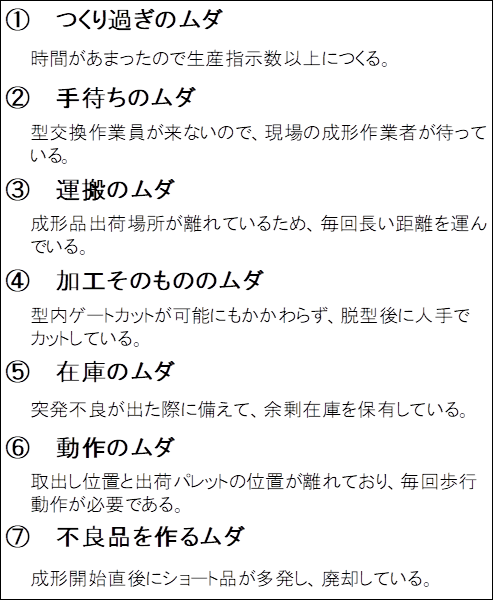
「手待ちのムダ」、これは、その言葉の通りで容易に理解できるところです。
「5回のなぜ」 実はトヨタ社内の現場では実施していない
さて、ムダを根元から断ち切るためには、その真の原因からの対策が必要です。
これも当たり前のことです。
その真因究明のためには、「5回のなぜ」による検討がなされます。
ちなみに、トヨタ社内では5回のなぜでの真因究明は実施していません。
日々の業務では5回のなぜを意識せずに、ごく当たり前のように、真因に行きつくまで検討を重ねる、これがトヨタの真のカイゼンなのです。
トヨタ社員は、真因究明がDNAとして染みついています。
日々の業務の中でのODJで身に付けています。
従って、わざわざ「5回のなぜ」を意識する必要もありません。
もちろん、5回という回数は無意味です。
真因に行きつくまで検討します。
3回の思考の積み重ねの場合もあれば、十数回を要することもあります。
トヨタ生産方式の導入の難しさ
これは、事あるごとに触れてきている点です。
前述の真因追求のための「5回のなぜ」で説明したように、トヨタ社員には、トヨタ生産方式やその推進のためのカイゼン魂がDNAとして染みついています。
その習得は基本、OJTです。
長い経験のもとに、良質のDNAとして進化します。
最終的には、誰でも同じ反応を示すDNAとなります。
これは重要な点です。
同じDNAを保有しているということは、前提条件や進め方に関しての議論が不要ということです。
また、誰が対応しても同じ最良の結果が得られることになります。
トヨタ生産方式を他社に導入することはきわめて不可能と考えます。
もちろん、導入して成功している会社もありますが、気の遠くなるほどの努力と年月の末に実現しています。
では、トヨタ生産方式の導入はどうすべきか?
これも事あるごとに触れてきている点ですが、まずは、導入の狙いの確認からです。
その目的に最も適したアプローチと手法の選定が必要です。
そのためには、手前味噌となりますが、我々コンサルタントに相談することが早道です。
手待ちのムダとは
だいぶ前置きが長くなりました。
手待ちのムダとは、必要な作業を実施するための条件が整わずに、作業が始められず、まさに手持ち無沙汰に待っている状態です。
- 組み立ててみたら納入品が不良であることがわかったため、良品到着を待っている
- 組立工程で、必要な部品が到着していないために組立ができない、
- 設備が故障したために、保全修理担当者を待っている、
- 大雪でトラックの到着が遅れて、工場全体が停止している
などなど、まさに枚挙にいとまがありません。
列挙した事例、なかなかに味があるように見えました。
見かけの対策と真因対策の説明に適しています。
最初の事例を見てみましょう。
納入品の不良に対して、どのような対策が必要でしょうか?
案① 万が一不良品が納入された際に、生産が停止しないように、あらかじめ良品を確保しておく。
⇒これは、如何にもトヨタ生産方式の考え方に反しますね。
在庫を持たない(現実には、論理的に考えた最小在庫)ことが信念ですから。
よって、在庫を持たなくても対応できる対策案が必要です。
案② 納入品検査で確実に良品のみを受け入れる。
⇒自社内の安全確保の視点では、一見、合理的な対策にも見えます。
しかし、不良が納入されないことが担保されれば、受け入れ検査が不要となり、検査対応工数や場所が不要となります。
これが理想です。
よって、選択すべき対策は「不良品が納入されない」ということになります。
案③ 仕入先が不良品を納入しないことを保証する。
⇒自社の守りとしては確実な対応です。
ただし、トヨタではここで終わりません。
真因追求のDNAにより、「なぜ不良品を出荷したのか」という仕入れ先の問題にまで踏み込んでいきます。
実はここが、トヨタのコスト最小化にも通じるところです。
仕入れ先において、不良が発生しない工程にまで生産方法を高めることができれば、
すなわちトヨタ生産方式に通じる真因追求の「5回のなぜ」が実践できれば、不良品を製造することはなくなります。
同時に、不良にかかわる原材料や加工エネルギー、あるいは検査が不要となり、納入品のコストが最小化することとなります。
案④ 仕入先での不良発生に対する真因対応
⇒前述のように、これが、取るべき最良の対策となります。
仕入先としては、その真因追求手法を自社のものとし、
他の製品や工程に横展開(この言葉も、トヨタが大好きな言葉です)できれば、
会社の収益構造をもカイゼンできることになります。
もちろん、大前提として、トヨタと仕入先との間で、
相互依存関係を合理的に理解し合っていることが必要となります。
他の「手待ちのムダ」の事例に関しても次回以降で解説してまいります。
自社向けセミナーのご希望や成形加工の課題など お問合せから、お気軽にご相談をください。