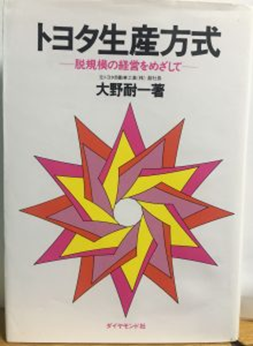
カイゼンの糸口として7つのムダの視点で観察します。
7つの着眼点をさかのぼるとトヨタ生産方式の骨子に行き着きます。
トヨタ生産方式の導入や、さらには継続のむずかしさに関してはしばしば解説してきているところです。
7つのムダの実践においても、本来的にはトヨタ生産方式の理解が必要です。
そのような背景を念頭に置きながら、7つのムダを見ていきます。
今回は 「手待ちのムダ」その2です。
大野耐一さん著の「トヨタ生産方式」の巻末には、付録の主要用語辞典がありますが、その中にも『ムダを意識し撲滅する』としてこの7つのムダを解説しています。
「トヨタ生産方式」by大野耐一 のご紹介
ぜひとも一度お読みいただきたい本です。
お買い求めのご参考までに、Amazonをご紹介します。
トヨタ生産方式――脱規模の経営をめざして | 大野 耐一 |本 | 通販 | Amazon
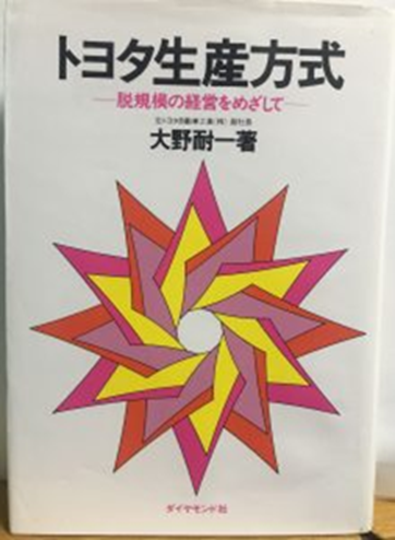
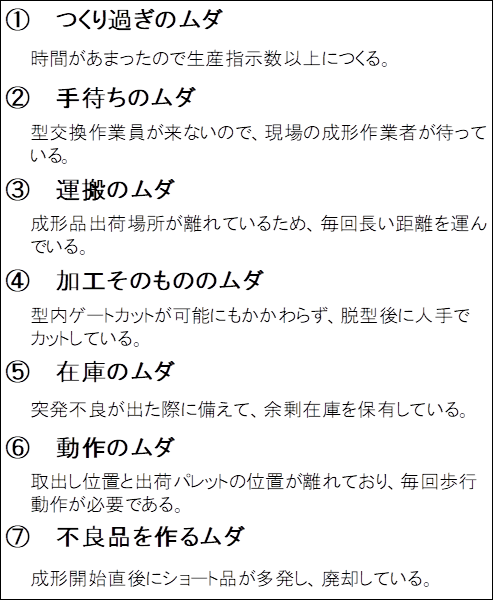
「手待ちのムダ」、これは、その言葉の通りで容易に理解できるところです。
前回は手待ちのムダとして以下の4例を紹介し、最初の例に関しての対応の着眼を解説しました。
- 組み立ててみたら納入品が不良であることがわかったため、良品到着を待っている
- 組立工程で、必要な部品が到着していないために組立ができない、
- 設備が故障したために、保全修理担当者を待っている、
- 大雪でトラックの到着が遅れて、工場全体が停止している
今回は残りの例に関して対応の着眼を解説します。
この着眼創出こそがTPSらしいアプローチの入り口です。ちゃんと入り口をくぐれればあとは手順に沿って検討対策するだけです。
「組立工程で、必要な部品が到着していないために組立ができない」 このあるべき対策は?
さて、この対策はなんでしょうか? その場での対応は、前工程に部品を取りに行く、あるいは、納入業者に出荷状況を確認するなどでしょうが、これそのものは当然カイゼンにはなりません。
やりがちな対応としては、到着遅れでも問題が無いように、あらかじめ手元に部品を確保するという手段です。これは最もやってはいけない対応です。中間在庫を持つということは、問題点をマスキングしてしまい、モノづくりの体力強靭化には全くつながりません。むしろ、中間在庫分の資本の滞留、在庫場所の確保、在庫の管理工数等まさにムダだらけです。
ではどうしましょうか?
まずは、到着しない原因、発生頻度、さらに被害度の情報を集めます。その上で「5回のなぜ」で到着しない「真因」を探ります。
2か月に一度、前工程で不良が多発して部品が供給できなくなるという状況が分かった場合、前工程の不良の撲滅が真のカイゼン対策です。自社の工程であり、カイゼンが根付いている職場の場合、それほど苦労せずに真の対策が可能となります。
難しいのは、納入部品であり。納入先の突発的な不良のケースです。納入先も含めてあるべき姿にカイゼンすることが望ましいのですが、納入先にその風土雰囲気が無い場合はどうしましょうか?
また、納入先からのトラックの交通事故が原因だった場合どのようなカイゼンが望ましいのでしょうか?
この辺りが、カイゼン実務の難しさです。
「設備が故障したために、保全修理担当者を待っている」 このあるべき対策は?
これも日常的に起きがちなトラブルです。すでに、前の例で、どのような対策とすべきかご理解いただけたかと思います。設備故障の真因を究明することが適切な対策です。現実には対策できないという言い訳、まあ難しさですが、これがたくさん出てきます。ここで以下に知恵を出すかです。「言い訳する前に知恵を出せ」 耳にタコができるくらい言われました、、笑
カイゼンが根付いている職場では、トラブルが起きる現場の作業者が、実によく設備トラブルの状況を観察しています。そして、自らカイゼン対応する、あるいはカイゼン提案するとの流れとなります。
職場の雰囲気も「天使のスパイラル」です。すなわちカイゼンが次のカイゼンを生み、どんどんと理想的な工程に作りこまれていきます。
「大雪でトラックの到着が遅れて、工場全体が停止している」 このあるべき対策は?
数年に一度のために全工程で余剰在庫を保有するなどはあり得ません。頻度問題ですが、数年に一度の大雪のケースは、やむを得ないと諦めましょう。
トヨタを辞して数年後に、当時の上司を訪問したことがあります。ちょうど、国内全体の生産統括の役員となってました。訪問は月曜日の午前中でしたが、ちょうど、週末に大雪で物流が止まる状況でした。恐る恐る訪問すると、「金曜夜に国内全ライン生産停止の指示をしたから、今は暇だぞ」と冗談半分で言われました。トヨタらしい大胆さであり、この大胆さがあるからこと、ち密なトヨタ生産方式が成り立つものと感心したことを覚えています。
自社向けセミナーのご希望や成形加工の課題など お問合せから、お気軽にご相談をください。